Industrial IoT Solutions: Software Development for Connected Factories and Machines
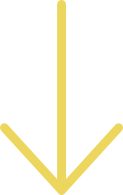
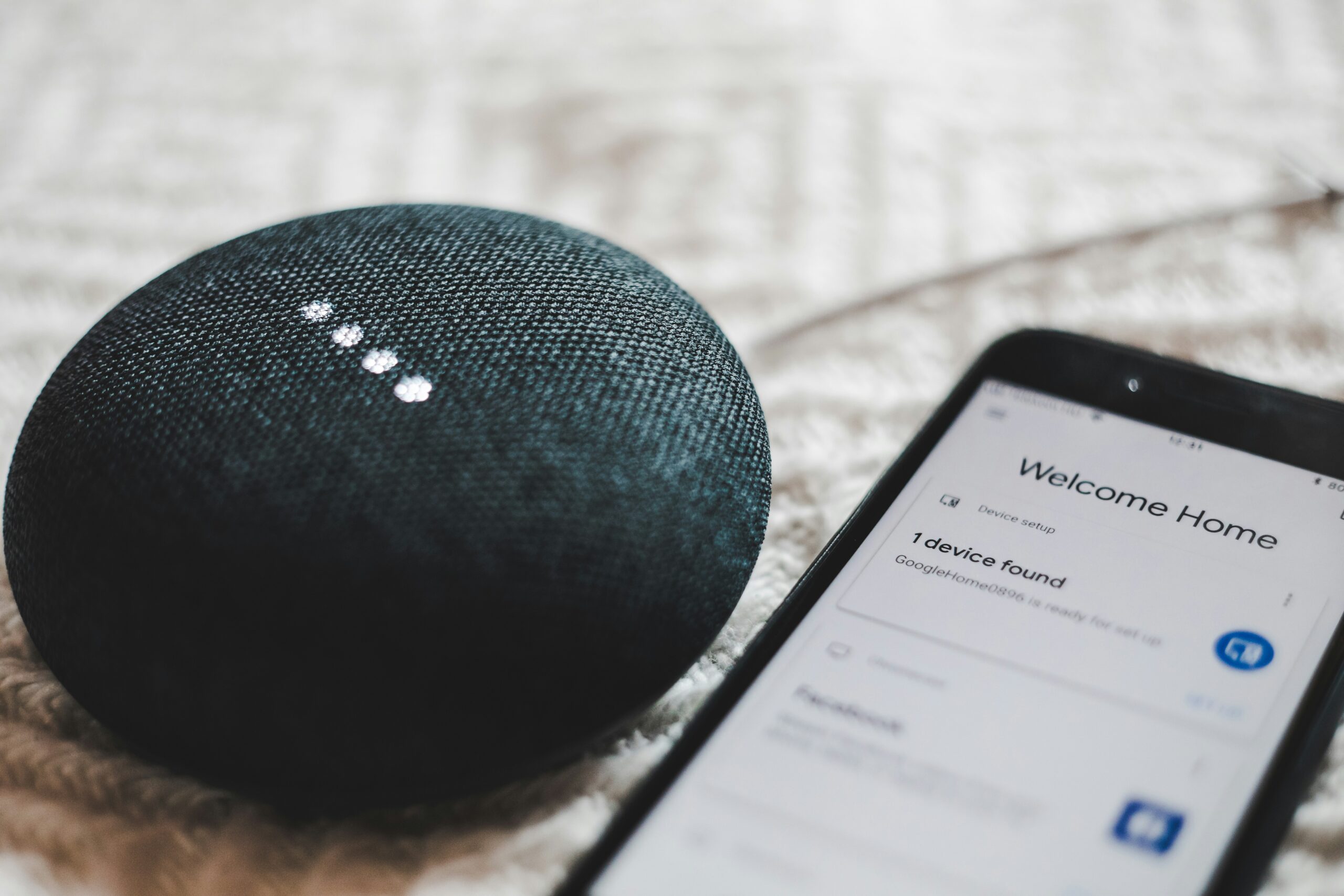
Forget the robots taking over – the real revolution in manufacturing is happening silently, through lines of code. Software is the hidden hand behind connected factories and machines, unlocking a world of data-driven insights, optimized production, and even predictive maintenance. For instance, using AWS IoT, industrial companies build predictive quality models that identify potential bottlenecks, failures, and quality issues before they occur. Let’s dive deep into the fascinating world of software development for the industrial age. We’ll explore how code is transforming factories, from the shop floor to the executive suite, and how it’s paving the way for a more efficient, sustainable, and intelligent future of manufacturing.
IIoT refers to the interconnected network of sensors, machines, devices, and software systems within industrial environments. These components collect and exchange data, enabling automation, monitoring, and optimization of various manufacturing processes. Unlike traditional manufacturing setups, IIoT leverages advanced technologies such as cloud computing, artificial intelligence (AI), and big data analytics to enhance efficiency, productivity, and decision-making capabilities.
The significance of IIoT in modern manufacturing cannot be overstated. By harnessing real-time data from machinery and production lines, manufacturers can achieve heightened levels of operational visibility and control. IIoT facilitates predictive maintenance, allowing businesses to preemptively address equipment failures, minimize downtime, and optimize asset utilization. Furthermore, IIoT enables the implementation of agile production methodologies, customization at scale, and seamless integration across supply chain networks, thereby enhancing flexibility and responsiveness to market demands.
Understanding Connected Factories and Machines
- What Constitutes a Connected Factory? A connected factory integrates various technologies and systems to create a seamless and data-driven manufacturing environment. It encompasses the interconnection of machinery, equipment, sensors, and software applications throughout the production process. Key components include IoT-enabled devices, industrial robots, programmable logic controllers (PLCs), and enterprise resource planning (ERP) systems. These elements work in tandem to facilitate real-time data exchange, automation, and optimization of manufacturing operations.
- Role of IoT Devices in Factory Connectivity: IoT devices play a pivotal role in establishing connectivity within factories. These devices are equipped with sensors that capture valuable data such as temperature, humidity, vibration, and energy consumption. By transmitting this data to centralized systems via wireless or wired networks, IoT devices enable continuous monitoring and analysis of equipment performance and production metrics. Moreover, IoT devices facilitate remote access and control, empowering manufacturers to oversee operations from anywhere in the world and respond promptly to emerging issues or opportunities.
The connectivity of machines in industrial settings yields a multitude of benefits for manufacturers:
- Enhanced Efficiency: Connected machines streamline production processes by minimizing manual intervention, reducing idle time, and optimizing resource utilization. This leads to higher throughput, shorter lead times, and lower production costs.
- Predictive Maintenance: By monitoring equipment condition in real-time, manufacturers can implement predictive maintenance strategies. IoT-enabled predictive maintenance helps prevent unplanned downtime by detecting potential faults or malfunctions before they escalate into costly failures.
- Data-Driven Decision Making: Connecting machines generates vast amounts of data that can be leveraged to gain actionable insights into production performance, quality issues, and process optimization opportunities. Analyzing this data empowers manufacturers to make informed decisions, identify areas for improvement, and drive continuous innovation.
- Agile Adaptation: Connected factories enable agile production processes that can quickly adapt to changing market demands, customer preferences, or supply chain disruptions. By facilitating rapid reconfiguration of production lines and workflows, manufacturers can maintain competitiveness in dynamic business environments.
Challenges in Developing IIoT Solutions
- Security Concerns in Industrial Environments: Security remains a paramount concern in the development of IIoT solutions. Industrial environments are particularly vulnerable to cyber threats due to the interconnected nature of devices and systems. Hackers may exploit vulnerabilities in IoT devices or networks to gain unauthorized access, disrupt operations, or compromise sensitive data. Addressing security concerns requires robust encryption protocols, authentication mechanisms, and intrusion detection systems to safeguard against cyber attacks and ensure the integrity and confidentiality of industrial data.
- Integration with Existing Systems and Legacy Equipment: Another significant challenge in developing IIoT solutions is the seamless integration with existing systems and legacy equipment. Many industrial facilities operate on legacy infrastructure that lacks native IoT capabilities, making integration complex and challenging. Developers must devise interoperable solutions that can interface with diverse protocols, communication standards, and proprietary technologies. Retrofitting legacy equipment with IoT sensors and communication modules may be necessary to enable data capture and connectivity, requiring careful planning and implementation to minimize disruptions to ongoing operations.
- Scalability and Interoperability Issues: Scalability and interoperability present additional hurdles in the development of IIoT solutions. As industrial operations expand or evolve, IIoT systems must scale seamlessly to accommodate growing volumes of data, devices, and users. Moreover, achieving interoperability across heterogeneous devices and platforms is essential for facilitating seamless communication and data exchange. Standardization efforts, such as the adoption of industry-wide protocols and communication standards, can help mitigate interoperability challenges and promote compatibility among disparate systems and devices.
Key Components of IIoT Software Development
- Edge Computing for Real-Time Data Processing: Edge computing plays a critical role in IIoT software development by enabling real-time data processing at the network edge, closer to the data source. This approach minimizes latency and bandwidth usage by processing data locally on IoT devices or gateways before transmitting it to centralized systems. Edge computing is particularly beneficial in industrial settings where milliseconds matter, facilitating timely decision-making, rapid response to events, and support for mission-critical applications such as predictive maintenance and quality control.
- Cloud Platforms for Data Storage and Analytics: Cloud platforms serve as the backbone of IIoT ecosystems, providing scalable infrastructure for data storage, processing, and analytics. By leveraging cloud services, IIoT developers can store vast amounts of sensor data securely, access advanced analytics tools, and derive actionable insights from disparate data sources. Cloud-based solutions enable manufacturers to harness the power of big data, machine learning, and AI algorithms to optimize production processes, improve efficiency, and drive innovation.
- Machine Learning and AI for Predictive Maintenance: Machine learning and AI algorithms play a pivotal role in predictive maintenance, a key application of IIoT in industrial settings. By analyzing historical data, sensor readings, and equipment telemetry, these algorithms can predict equipment failures, identify anomalous behavior, and recommend proactive maintenance actions. Predictive maintenance minimizes unplanned downtime, extends equipment lifespan, and reduces maintenance costs, leading to improved asset reliability and operational efficiency.
- User Interfaces for Monitoring and Control: User interfaces serve as the primary means for operators to monitor and control IIoT systems in industrial environments. Intuitive dashboards, visualization tools, and control panels enable operators to visualize real-time data, track performance metrics, and interact with connected devices and machinery. User interfaces should be designed with usability and efficiency in mind, providing actionable insights and enabling quick decision-making to optimize production processes and ensure seamless operation of IIoT-enabled systems.
Best Practices for Developing IIoT Software
- Prioritizing Security from the Ground Up: Security should be a primary consideration in every stage of IIoT software development. Implementing security measures from the outset, including encryption, authentication, and access control mechanisms, helps mitigate cyber threats and safeguard sensitive industrial data. Developers should adhere to industry best practices, conduct regular security audits, and stay abreast of emerging threats to ensure the resilience and integrity of IIoT systems.
- Building Modular and Scalable Architectures: IIoT software should be designed with modularity and scalability in mind to accommodate evolving business needs and technological advancements. Adopting a modular architecture facilitates component reuse, code maintainability, and extensibility, enabling developers to add new features or integrate with third-party systems seamlessly. Scalable architectures allow IIoT solutions to grow organically with the expansion of industrial operations, ensuring performance and reliability at scale.
- Implementing Robust Data Management Strategies: Effective data management is essential for harnessing the full potential of IIoT systems. Developers should devise robust strategies for collecting, storing, processing, and analyzing data generated by connected devices and sensors. This entails defining data models, establishing data governance policies, and deploying scalable data storage solutions. Furthermore, implementing data quality assurance measures and data lifecycle management practices ensures the accuracy, integrity, and usability of industrial data for informed decision-making.
- Continuous Testing and Monitoring for Reliability: Continuous testing and monitoring are crucial for ensuring the reliability and resilience of IIoT software in industrial environments. Developers should conduct rigorous testing throughout the development lifecycle, including unit testing, integration testing, and performance testing, to identify and address software defects and performance bottlenecks. Additionally, implementing real-time monitoring and analytics enables proactive detection of anomalies, performance degradation, or security breaches, facilitating timely intervention and maintenance to minimize disruptions to production processes.
Case Studies of Successful IIoT Implementations
- Example 1: Predictive Maintenance System in an Automotive Factory: An automotive factory implemented a predictive maintenance system leveraging IIoT technologies to enhance equipment reliability and minimize downtime. By equipping machinery with sensors to monitor key performance indicators such as temperature, vibration, and fluid levels, the system continuously collected data on equipment health. Machine learning algorithms analyzed this data to identify patterns indicative of potential failures, enabling proactive maintenance interventions before critical issues occurred. As a result, the automotive manufacturer achieved significant cost savings by reducing unplanned downtime, extending equipment lifespan, and optimizing maintenance schedules.
- Example 2: Remote Monitoring Solution for Oil and Gas Equipment: An oil and gas company deployed a remote monitoring solution powered by IIoT to monitor the condition and performance of equipment across remote drilling sites and refineries. IoT sensors installed on pumps, valves, and pipelines transmitted real-time data on operational parameters such as pressure, flow rate, and temperature to centralized monitoring systems. This enabled engineers to remotely monitor equipment health, detect anomalies, and identify potential maintenance needs before they escalated into costly failures or safety incidents. By leveraging IIoT for remote monitoring, the oil and gas company improved operational efficiency, reduced maintenance costs, and enhanced worker safety across its facilities.
- Example 3: Optimization of Production Processes in a Food Processing Plant: A food processing plant implemented IIoT-enabled sensors and analytics to optimize production processes and ensure product quality. By monitoring factors such as temperature, humidity, and airflow in production facilities, the system identified opportunities for process optimization and quality control. Machine learning algorithms analyzed real-time data to optimize recipe formulations, minimize waste, and ensure compliance with regulatory standards. Additionally, the plant utilized IIoT data to track and trace products throughout the supply chain, enhancing transparency and traceability. As a result, the food processing plant achieved improved product consistency, reduced production costs, and enhanced customer satisfaction.
Future Trends in IIoT Software Development
- Expansion of Edge Computing Capabilities: Edge computing is poised to play an increasingly vital role in IIoT software development, with a growing emphasis on pushing intelligence closer to the data source. As the volume of data generated by IoT devices continues to skyrocket, edge computing enables real-time processing and analysis of data at the network edge, minimizing latency and bandwidth usage. Future advancements in edge computing will likely include greater integration with AI algorithms for edge-based analytics, enhanced support for resource-constrained devices, and improved edge-to-cloud orchestration for seamless data management across distributed environments.
- Integration of Blockchain for Secure Data Transactions: Blockchain technology holds promise for enhancing the security and integrity of IIoT data transactions in industrial settings. By leveraging distributed ledger technology, blockchain enables immutable and transparent record-keeping, ensuring the authenticity and provenance of data exchanged between interconnected devices and systems. In the future, we can expect to see increased adoption of blockchain for securing IIoT data transactions, establishing trust among stakeholders, and enabling secure peer-to-peer communication and transactions across industrial supply chains.
- Advancements in AI-Driven Automation: AI-driven automation is poised to revolutionize IIoT software development, enabling autonomous decision-making and adaptive control in industrial environments. Future advancements in AI will focus on enhancing machine learning algorithms for predictive analytics, anomaly detection, and prescriptive insights. This will enable IIoT systems to autonomously identify and address operational inefficiencies, optimize production processes in real-time, and adapt to dynamic market conditions. Moreover, AI-driven automation will facilitate human-machine collaboration, empowering workers with AI-enabled tools and insights to drive continuous improvement and innovation.
- Standardization Efforts for Interoperability: Standardization will be crucial for ensuring interoperability and compatibility among diverse IIoT devices, platforms, and systems. Future trends in IIoT software development will see increased emphasis on standardization efforts, including the development of industry-wide protocols, communication standards, and data models. Standardization initiatives aim to simplify integration challenges, promote seamless interoperability across heterogeneous environments, and facilitate the exchange of data and insights among interconnected devices and systems. By embracing standardization, IIoT developers can accelerate innovation, reduce implementation complexities, and unlock the full potential of interconnected industrial ecosystems.
Drive Continuous Improvement
IIoT represents a paradigm shift in industrial manufacturing, offering unprecedented opportunities for innovation, efficiency, and competitiveness. By leveraging interconnected networks of sensors, machines, and software systems, IIoT enables real-time data exchange, automation, and optimization of manufacturing processes. From predictive maintenance and remote monitoring to production process optimization, IIoT empowers businesses to enhance operational visibility, minimize downtime, and drive continuous improvement initiatives.
Ready to elevate your brand and transform your vision to digital solutions? Since 2003, StudioLabs has been trusted to help conceive, create, and produce digital products for the world’s most well-known brands to cutting-edge startups. Partner with StudioLabs and create something phenomenal. Let’s chat and experience StudioLabs in action with a complimentary session tailored to your business needs!